Rozmawiał Jerzy Przywara
Od pieca do pieca
Sama geodezja to za mało. Trzeba umieć znaleźć się przy modernizacjach, projektowaniu czy ekspertyzach, i to nie gdzieś na dole, ale na poziomie szczebla zarządzającego – mówią właściciele firmy Geoservex z Bydgoszczy Bolesław Krystowczyk i Zbigniew Krystowczyk w najnowszym wydaniu GEODETY.
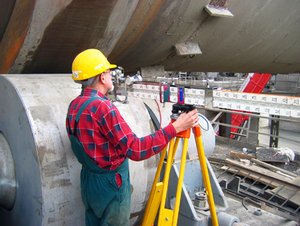 fot. ze zbiorów firmy Geoservex
JERZY PRZYWARA: Na ścianach panów gabinetu wiszą liczne dyplomy i wyróżnienia...
BOLESŁAW KRYSTOWCZYK: Kiedyś bawiliśmy się w różne konkursy, ale daliśmy sobie spokój, bo były z tym tylko kłopoty i wielu chętnych na „sponsorowanie” nagrody.
ZBIGNIEW KRYSTOWCZYK: Niezamierzony efekt uboczny był taki, że po każdym laurze dzwoniły... banki, oferując swoje konta i usługi. A nasi klienci i tak nie wiedzieli, co to za nagroda.
Od początku działalności firmy zajmujecie się geodezyjną obsługą pieców obrotowych w cementowniach.
BK: Skoncentrowaliśmy się na rynku obsługi tych maszyn i jesteśmy w ścisłej czołówce światowej, chociaż w Polsce mało kto o tym wie.
ZK: Naszym kluczowym produktem jest obsługa geodezyjna maszyn obrotowych, przede wszystkim pieców, a tych najwięcej jest w przemyśle cementowym. Piec to serce cementowni i najbardziej obciążona maszyna, która podlega deformacjom o wiele częściej niż podobne urządzenia w przemyśle mineralnym czy papierniczym. Piece to także najbardziej wartościowe aktywa zakładu. W związku z tym kierownictwo cementowni łatwiej podejmuje decyzje o skrupulatnym sprawdzaniu i serwisowaniu tych maszyn.
Początki przygody z cementowniami sięgają końca lat 70.
BK: Tak się złożyło, że w OPGK Bydgoszcz, gdzie zjawiłem się jeszcze jako student, dyrektor wysłał mnie do cementowni, żebym zajął się piecem. Od razu bardzo mnie to zainteresowało. Po dyplomie spotkałem na swojej drodze prof. Bogdana Neya, który bezbłędnie wyczuł ciekawy temat i namówił mnie do zrobienia doktoratu. Następnie trafiłem do prof. Wojciecha Janusza, który pomógł mi to wszystko usystematyzować. Recenzentami pracy doktorskiej, obronionej w 1983 roku, byli prof. Jan Gocał i prof. Witold Prószyński. Znakomita szkoła, najlepsze nazwiska. W połowie lat 80. w OPGK zająłem się piecami na poważnie, potem została wydzielona specjalna pracownia, a gdy przyszła transformacja, założyliśmy wraz z inżynierem Wiesławem Pauszkiem własną firmę. Tak w 1991 r. powstał Geoservex. A Zbyszek od dziecka był zafascynowany piecami [patrz okładka – red.], jako starszy chłopak często towarzyszył mi w pracy i było oczywiste, że skończy studia geodezyjne i dołączy do firmy.
Czy wkraczacie do cementowni dopiero wtedy, gdy piec ulega deformacji?
ZK: Już w czasie budowy jest prowadzony nadzór nad montażem. To są maszyny, których średnica dochodzi do siedmiu metrów, a długość do stu – przy nowszych konstrukcjach i stu kilkudziesięciu – przy starszych. Ta rura musi być złożona z dokładnością 1-2 milimetrów. Montaż zwykle nadzoruje producent, ale zdarza się, że klient zamawia naszą usługę, na przykład gdy piec jest składany z elementów dostarczanych przez różnych producentów lub gdy niektóre elementy są adaptowane ze starej konstrukcji.
Co faktycznie oferujecie klientowi?
BK: Jako pierwsi na świecie wprowadziliśmy metodę osiowania pieców w czasie ich ruchu. W 1985 roku to była rewolucja. Kiedy podczas pierwszej regulacji przesuwaliśmy rolki, na których opiera się piec, wszyscy inni spod tej gorącej maszyny uciekali. Amerykanie nazwali naszą metodę hot kiln alignment i termin wszedł do światowego słownictwa technicznego. Profesor Witold Prószyński powiedział mi kiedyś, że miałem podwójne szczęście. Po pierwsze, że doszedłem do tego nie na drodze naukowej, tylko praktycznej, a po drugie, że ten pierwszy piec się nie zawalił. Rzeczywiście wiązało się z tym wielkie ryzyko. Metodę zastosowaliśmy najpierw w polskich cementowniach, później w byłym bloku krajów socjalistycznych.
Jakie były dalsze kroki w rozwoju tej technologii?
BK: Następną nowością było wykorzystanie dalmierza laserowego Disto. Pierwszy pomiar przeprowadziliśmy w Słowenii w 1989 roku. Za pomocą Disto mierzyliśmy w trybie ciągłym odległość do obracającego się pieca. Można powiedzieć, że to było skanowanie w 2D.
ZK: Początkowo rejestracja wyników odbywała się ręcznie, ale Disto mierzyło odległości szybciej, niż my byliśmy w stanie pisać. Dlatego zawczasu przygotowywaliśmy specjalne formularze i jeden człowiek stał ze stoperem, a drugi wypełniał rubryki. Szybko jednak zaczęliśmy opracowywać system rejestrujący. Wykorzystaliśmy do tego znany w geodezji rejestrator Psion LZ64. Ku naszemu zdziwieniu jego procesor też nie nadążał z zapisywaniem rekordów! Dzisiaj zarejestrowanie 600 odczytów w czasie jednego obrotu pieca nie sprawia żadnych problemów.
A z najnowszych osiągnięć, czym byście się pochwalili?
BK: Projektowaniem od tyłu, czyli modelowaniem istniejącego obiektu na podstawie dokładnych pomiarów. Dzisiaj buduje się stosunkowo niewiele cementowni, głównie modernizuje się istniejące. Wygląda to tak, że np. stary 8-podporowy piec tnie się na pół i na tej bazie robi nowy – wydajniejszy i krótszy. Konieczne jest wtedy połączenie starego projektu z nowym, czyli starych części z nowymi. Prowadząc analizę od tyłu, pomagamy określić prawidłowe parametry takiego urządzenia.
ZK: Wspólnie z ekspertami związanymi z Wydziałem Mechaniki Energetyki i Lotnictwa Politechniki Warszawskiej opracowaliśmy specjalne oprogramowanie do określania parametrów mechanicznych pieców obrotowych. Najpierw wykonujemy pomiar maszyny, a potem wyliczamy odpowiednie parametry i sprawdzamy, czy spełniają one normy dokładnościowe. Dotyczy to zarówno geometrii, jak i mechaniki (np. czy nie są przekroczone naprężenia albo czy łożyska są właściwie obciążone). Powstaje trójwymiarowy model maszyny. Mając wiedzę o rodzaju materiałów, z jakich jest zrobiona, wyliczamy obciążenia i naprężenia w powłokach i korpusie pieca. Warto też wspomnieć o wykorzystaniu algorytmów statystycznych do obliczania ekscentrów itd. Niedawno zmierzyliśmy się z problemem wizualizacji wyników. Przez wiele lat stosowaliśmy do tego celu zwykłe rysunki (przekroje radialne albo aksonometryczne). Ale gdy do użytku weszła grafika komputerowa, aż się prosiło, żeby pokazać wyniki w 3D. Przygotowaliśmy odpowiedni format naszych danych i opracowaliśmy najważniejsze założenia. Dane do wizualizacji mają być zapisywane w pliku, który można wysłać do biura przez internet nawet za pomocą telefonu komórkowego, wizualizacja w 3D musi być gotowa najpóźniej w ciągu 24 godzin, a plik wynikowy musi być na tyle mały, by można go było odebrać z biura także za pomocą komórki. Po pół roku pracy okazało się, że stworzenie ruchomego modelu wiąże się ze stosowaniem drogiego oprogramowania graficznego i plikiem tak dużym, że o jego otwarciu na 10-letnim komputerze naszego klienta np. w Pakistanie nie ma mowy. Ale nie daliśmy za wygraną i w końcu udało nam się zaadaptować darmowe oprogramowanie Adobe Reader. Najpierw robimy modelowanie, a potem film (32 klatki na sekundę). Klient ogląda model pieca w skali i widzi wszystkie jego deformacje i ekscentry. Rura na ekranie się kręci, a plik ma zaledwie 400 kB!
To znacznie więcej niż czysta geodezja.
BK: Na pewno skręciliśmy w stronę mechaniki i ekspertyz. „Sama geodezja” to za mało. Trzeba umieć znaleźć się przy modernizacjach, projektowaniu czy ekspertyzach, i to nie gdzieś na dole, ale na poziomie szczebla zarządzającego. Kiedyś Polska była potęgą w geodezji inżynieryjno-przemysłowej, wystarczy wspomnieć szkołę prof. Wojciecha Janusza czy doświadczenia z obsługą turbin zespołu dr. Mirosława Żaka. Od tego czasu właściwie zostaliśmy tylko my. Pomiary turbin czy maszyn papierniczych przechwycili mechanicy. Oddaliśmy to, tak jak i inne działy geodezji.
ZK: Faktem jest, że z geodezji inżynieryjno-przemysłowej zniknęło wiele aktywności. Ale trudno winić za to geodetów. Oprzyrządowanie pomiarowe jest coraz dokładniejsze i coraz łatwiejsze w obsłudze. Urządzenia laserowe, sensory są tak zaawansowane, że geodeta staje się często niepotrzebny. Kiedyś przy obsłudze maszyny papierniczej zadaniem geodety było znalezienie linii odniesienia i pomiar setek wałków w układzie tej linii. I co się nagle stało? Wynaleziono system inercyjny, który wykorzystuje pole magnetyczne Ziemi i siłę Coriolisa. Urządzenie kładzie się na wał, przejeżdża nim w jedną i drugą stronę, i gotowe. Mamy jednolity układ? Mamy! Trzeba się dowiązywać? Nie! Eliminuje nas technologia. Gdyby nasza firma pozostała tylko przy samych pomiarach, to mechanicy też by nas wyeliminowali. Dzisiaj nie wystarczy znać geometrię maszyny, ale trzeba zarekomendować klientowi rozwiązanie, które usprawni pracę jego zakładu.
Czy wasze wyliczenia zawsze sprawdzają się w praktyce?
ZK: Bywa tak, że z geometrią jest wszystko w porządku, a korpus pieca nadal pęka, choć jest zrobiony z blachy o grubości 40 mm. Wtedy wchodzimy w mechanikę maszyny i badamy, który parametr został przekroczony. Zdarzają się przypadki, że projektanci oszczędzają na materiałach albo specyfika złoża materiałowego jest inna niż w projekcie i wewnątrz pieca kumuluje się nadmiar tzw. napieku, a może się go tam dodatkowo odłożyć nawet 100 ton. Czasami parametry pieca są przewidziane dla zwykłej ogniotrwałej cegły, ale po jakimś czasie zastosowano w nim cegłę magnezytową, która jest o wiele cięższa. To powoduje, że elementy, które powinny bez problemów wytrzymać założone obciążenia, ulegają uszkodzeniu. Bierzemy też pod uwagę parametry dynamiczne, na przykład związane z nierównomiernym wygrzaniem korpusu. W takim przypadku przy każdym obrocie obciążenie podpory pieca może się zwiększyć o 30-40%, a jak coś pójdzie nie tak, to i o 100%. Łożysko, które powinno wytrzymać ciśnienie 4,4 MPa, jest okresowo dociążone podwójnie. Znając parametry mechaniczne, analizujemy, co zrobić z geometrią, żeby ten stan poprawić.
To wszystko załatwia oprogramowanie?
ZK: Choć software robi pełną analizę, to nie on decyduje o tym, o ile obniżyć podporę. Porównujemy parametry z tolerancjami i sprawdzamy, jakie jest ich procentowe wykorzystanie. Z doświadczenia wiemy, że jeżeli w trzypodporowym piecu obniżymy podporę środkową o 4 mm, to obciążenie na niej zmniejszy się o 7-8%, a na sąsiednich zwiększy o 3-4%. Jeśli więc obciążenie na bocznych podporach jest już na skraju tolerancji, to obniżenie środkowej nie wchodzi w grę, ale jeśli jest na poziomie 80% tolerancji, to operacja jest możliwa i wykonujemy odpowiednią analizę. W literaturze nazywa się to stiffness matrix (macierz sztywności), czyli macierz zawierająca 9 parametrów, które są niczym innym jak procentową zmianą obciążenia. Standardowo analizujemy obniżenie o 10 mm w interwałach co 2 mm. Ponadto sprawdzamy, jaka będzie reakcja korpusu na naprężenia zginające. Przy okazji warto też wspomnieć o cyklicznych wychyleniach. Umieszczając czytnik cyfrowy pod rolkami, widzimy, jak one pracują. Jeśli ugina się rolka, to ugina się także podpora, na której stoi nasz człowiek z instrumentem. Nie możemy tego pominąć. I dlatego drugi geodeta, sprawdza, co się „dzieje” ze stanowiskiem pierwszego obserwującego tworzącą pierścienia.
Nieodłącznym elementem pracy takich maszyn są drgania podłoża. Jak sobie z nimi radzicie?
BK: Osoba niewprawna nie spoziomuje w takich warunkach instrumentu. W pobliżu turbiny niwelatory samopoziomujące wpadają w rezonans i nie można wykonać odczytu. Natomiast doświadczony obserwator poradzi sobie z niwelatorem libelowym. Trzeba też wiedzieć, że nie wszędzie w pobliżu maszyny drgania są tak samo silne i przy pewnej praktyce daje się to wyczuć.
A co z wysoką temperaturą?
ZK: Jeśli jest bardzo gorąco, mam tylko jedną radę: mierzyć szybko. Podczas szkolenia mówię młodym inżynierom, że jeśli znoszą temperaturę przy piecu, to i instrument ją zniesie, ale jeśli mają już dość, to niech uciekają razem z instrumentem, bo on też nie wytrzyma.
Czasami zamiast świadczyć usługi, sprzedajecie klientowi technologię. Czy to nie jest podcinanie gałęzi, na której siedzicie?
ZK: Decyduje rachunek ekonomiczny. Do pewnego momentu to się nie opłaca, bo strumień pieniądza, który pochodzi z serwisu, jest wystarczająco duży. Ale jeśli okazuje się, że sprzedaż technologii wygeneruje dużo więcej pieniędzy niż trzyletni serwis, to sprawa jest do przemyślenia. Oczywiście sprzedaż technologii jest obwarowana pewnymi klauzulami ograniczającymi korzystanie z licencji tylko na określonym rynku, bez prawa odsprzedaży itd.
Czy ci, którzy kupili technologię, wracali do was po usługi, bo na przykład przeliczyli się z siłami?
BK: W 2001 roku sprzedaliśmy technologię instytutowi materiałów budowlanych w Indiach [patrz GEODETA 4/2002 – red.]. Okazało się, że wdrożenie w tamtejszych warunkach nie jest takie łatwe i ówczesna ekipa z Indii sobie z tym nie poradziła. Po 10 latach wracamy na ten rynek. Właśnie uruchamiamy swój oddział w Indiach, ale naszymi partnerami są już inni ludzie.
Gdzie jeszcze jesteście obecni?
BK: Mamy też oddział w Republice Południowej Afryki. Zaczynaliśmy tam 15 lat temu, potem zapadła cisza i teraz temat się odrodził. Zainteresowani są także Niemcy, trzeci producent urządzeń dla przemysłu cementowego na świecie. Ostatnio mieliśmy obiecujące pytania z Rosji. Zobaczymy, jak potoczą się negocjacje. Za kilka lat czekać będzie na nas cała Afryka, bo to rozwojowy rynek. Pracowaliśmy już w RPA, Etiopii i Kenii, Tanzanii, Libii i Algierii. Poza Australią i Ameryką Południową byliśmy na wszystkich kontynentach.
A jak jest w Europie?
BK: W Europie prawie wszystko już zbudowano, cementu trzeba niewiele, a cementownie ze względu na ochronę środowiska są zamykane.
ZK: Produkcja nie idzie pełną parą, maszyny są eksploatowane okresowo, a poziom techniczny obsługi jest tak wysoki, że nie dochodzi do jakichś większych awarii. Poza tym jest kilka firm oferujących usługi podobne do naszych. Na szczęście na rynku globalnym wygląda to nieco inaczej. Wydaje mi się, że jesteśmy bardziej elastyczni od firm zachodnich. Choć nasze stawki są tylko nieznacznie niższe, to dajemy bardziej konkurencyjną ofertę.
Ale działalność waszej firmy nie kończy się na obsłudze zagranicznych pieców?
BK: Eksport to 70% naszej sprzedaży, pozostałą część daje „normalna” geodezja. Obsługiwaliśmy m.in. budowę dachu stadionu Stade de France w Paryżu zbudowanego na mistrzostwa świata w piłce nożnej w 1998 roku, wykonujemy pomiary przemieszczeń elektrowni wodnych w północnej Polsce. Ostatnio prowadziliśmy obsługę budowy dachu w Operze Leśnej w Sopocie i to była fantastyczna sprawa. Główne części konstrukcyjne stanowiły dwie olbrzymie wygięte rury. Problem polegał na przejściu z układu projektowego na układ geodezyjny. W tym celu zrobiliśmy nawet plastikowy model takiej rury.
ZK: Dane dla montażystów podawano albo na łuku, albo w mierze kątowej i odnosiły się do osi rury, a ponadto każdy moduł był niezależnym układem. Żeby z milimetrową dokładnością wyznaczyć położenie króćców służących do mocowania lin, musieliśmy mieć segmenty w lokalnym układzie kartezjańskim, więc każdy z nich inwentaryzowaliśmy i za pomocą nakładania modeli sprawdzaliśmy, czy poszczególne moduły do siebie pasują. Dopiero wtedy taki element jechał na budowę, bo trudno wyobrazić sobie poprawianie położenia spawanego elementu ważącego 200 kg i wiszącego 30 metrów nad ziemią.
Jakich pracowników sobie dobieracie?
ZK: Średnia wieku naszej kadry wynosi około 35 lat, w większości inżynierowie, absolwenci AGH lub Politechniki Warszawskiej, wszyscy znają języki obce i są nawykli do podróżowania. Był taki okres, że większość stanowili młodzi ludzie, ale to się nie sprawdziło.
BK: Swego czasu w GEODECIE ukazała się rozmowa z Dariuszem Kowalikiem obsługującym budowę Świątyni Opatrzności w Warszawie. Fantastyczny człowiek, który uczestniczył w zarządzaniu tym projektem. Poradził sobie na budowie z inwestorem, projektantem i proboszczem. Mamy u siebie kilku takich „Kowalików”. Jak ten czy ów gdzieś pojedzie, to od razu próbuje kierować cementownią (śmiech).
Czy używacie innych instrumentów niż typowo geodezyjne?
BK: Adaptujemy różne instrumenty i urządzenia na potrzeby pomiarów. Pierwszym naszym wynalazkiem było sprzęgnięcie instrumentów geodezyjnych z czujnikiem zegarowym mierzącym przemieszczenia i przesunięcia z dokładnością do 0,01 mm.
ZK: Pewny pomiar odległości umożliwia nam łata inwarowa z układem mikrometrycznym pozwalająca na obserwację tworzącej pierścienia maszyny. Do tego oczywiście czujnik cyfrowy sprzężony z rejestratorem i... pirometr radiacyjny, bo równolegle wykonuje się pomiar temperatury komponentów maszyny (osiąga ona 350-400º C). Potem dane są redukowane do 20º C, by można je było porównać z projektowymi.
Wygląda na to, że działalność waszej firmy to pasmo sukcesów.
BK: Jeśli nie liczyć tego, że walkę z Urzędem Skarbowym w Bydgoszczy okupiłem zawałem serca, to można tak powiedzieć.
Przecież państwo mamy przyjazne przedsiębiorcom.
BK: Zwykłe zawracanie głowy. Działamy głównie za granicą, więc mamy liczne kontakty z polskimi konsulatami i ambasadami, które zamiast pomagać, żądają od nas sprawozdań, po co tam jesteśmy, co robimy, dla jakich klientów itd. Przez te wszystkie lata tylko jeden człowiek (konsul w Montrealu) faktycznie pomógł nam w potrzebie.
ZK: Nie bez przyczyny jesteśmy w ogonie światowego rankingu państw przyjaznych dla przedsiębiorcy. Praktycznie z każdej strony tylko obciążenia podatkowe i utrudnianie działalności. Niby mamy podpisane konwencje o unikaniu podwójnego opodatkowania, ale ten mechanizm nie działa. Jesteśmy łupieni na przykład przez rząd indyjski i ukraiński. W jaki sposób mamy się przed tym bronić? Czy mamy się procesować z rządami Indii, Ukrainy i Polski? Jako spółka cywilna nie możemy uzyskać od urzędu skarbowego tzw. certyfikatu rezydencji. Taki dokument może dostać tylko osoba fizyczna lub prawna. Jak mam wytłumaczyć zagranicznemu klientowi, że firma nie ma osobowości prawnej i urząd skarbowy nie zgodził się nawet na dopisanie na dokumencie wystawionym dla mnie jako osoby fizycznej adnotacji „wspólnik w spółce cywilnej Geoservex”? Dlatego klient mówi: to ja muszę ci potrącić podatek, bo nie jesteś w stanie udowodnić, że działasz na terenie Polski.
Jakie jeszcze niespodzianki czekają przy prowadzeniu takiego biznesu?
ZK: Pogorszyła się też sytuacja globalna i chyba nikt nikomu już nie ufa. Wzmożona kontrola nad przepływem transferów sprawiła, że czas przesłania pieniędzy z jednego kraju do drugiego bardzo się wydłużył, co utrudnia działalność. Od wykonania kontraktu do momentu zapłaty upływa zwykle wiele miesięcy. Obsługujemy takie kraje, jak Iran czy Irak, i bywa, że europejski bank obsługujący transfer odmawia przyjęcia płatności. Bez sprawdzenia, czy to jest legalny pieniądz, czy też nie.
To są uroki prowadzenia zagranicznych kontraktów.
ZK: Najpierw jest niezła gimnastyka z uzyskaniem w terminie wiz, potem ze sprawami podatkowymi, a na końcu z transferem pieniędzy. Oczywiście są kraje trudne, jeśli chodzi o logistykę i obsługę przedsiębiorcy, są i bardzo przyjazne. Na przykład Gruzja to miejsce do robienia interesów: wizę załatwia się na lotnisku, sprzęt można przywieźć ze sobą, nie trzeba wysyłać przez cargo, a procedura celna jest bardzo uproszczona. Bardzo trudne jest skoordynowanie pracy naszych zespołów, obsługują bowiem ponad czterdzieści krajów. Standardowy wyjazd trwa 2 tygodnie (tyle trzeba na pomiar jednego pieca), ale jeśli biegną nadzory nad remontami czy montażem, zajmuje to miesiące.
Czy wszędzie zgodzicie się pracować?
ZK: Nie. Kryterium jest takie: nie pracujemy w krajach, do których wstrzymano loty lub odmówiono wiz, co oznacza, że panuje tam konflikt zbrojny lub zerwano stosunki dyplomatyczne. Choć zdarzyło się i tak, że do Karbali (Irak) nasi ludzie dolecieli normalnie, ale na miejscu musieli założyć kamizelki kuloodporne i poruszali się w uzbrojonym konwoju.
Czy sami też jeździcie na pomiary?
BK: Na początku, gdy trzeba było wszystko rozkręcić, jeździłem bardzo często, podobnie później Zbyszek. Dzisiaj zdarza się to o wiele rzadziej.
ZK: Teraz najczęściej jeżdżę biznesowo, bo nie da się wszystkiego załatwić mailem, trzeba poznać ludzi. Mamy tu na miejscu pracownika zajmującego się logistyką, więc bez nas interes też się kręci, poza tym jesteśmy skomputeryzowani i nawet gdy przebywam za granicą, mogę o dowolnej porze odebrać wiadomości z serwera.
O ile jest łączność internetowa.
ZK: Akurat z tym nie ma problemu, bo obsługujemy duże obiekty przemysłowe. Mieliśmy niedawno kontrakt w Kenii, zakwaterowano nas nie w hotelu, tylko na kampie pod palmami niedaleko Mombasy. Spytałem menedżera, gdzie można podłączyć się do internetu, na co on odpowiedział, że internet jest wszędzie. Ponieważ nie dowierzałem, wyjaśnił, że mają wi-fi. No ale gdzie jest to wi-fi – dopytywałem się, na co on wskazał na jedną z palm, na której wisiał owinięty w folię punkt dostępowy.
Ale nie wystarczy mieć tachimetr, parę czujników i internet, by zacząć taki interes?
BK: Nie. Bo te piece, te maszyny trzeba jeszcze polubić. Są ludzie, którzy się ich boją. Jak się wchodzi na górę, to całość drga, jest niemiłosiernie gorąco, do tego wszystko jest zabrudzone smarami, pokryte rdzą. Ale patrząc od środka – działa jak szwajcarski zegarek.
Rozmawiał Jerzy Przywara
powrót
|